How to make your own Ethernet cable
You can make your own Ethernet cable to achieve lengths that are more useful and save some money in the long run. Here's how.
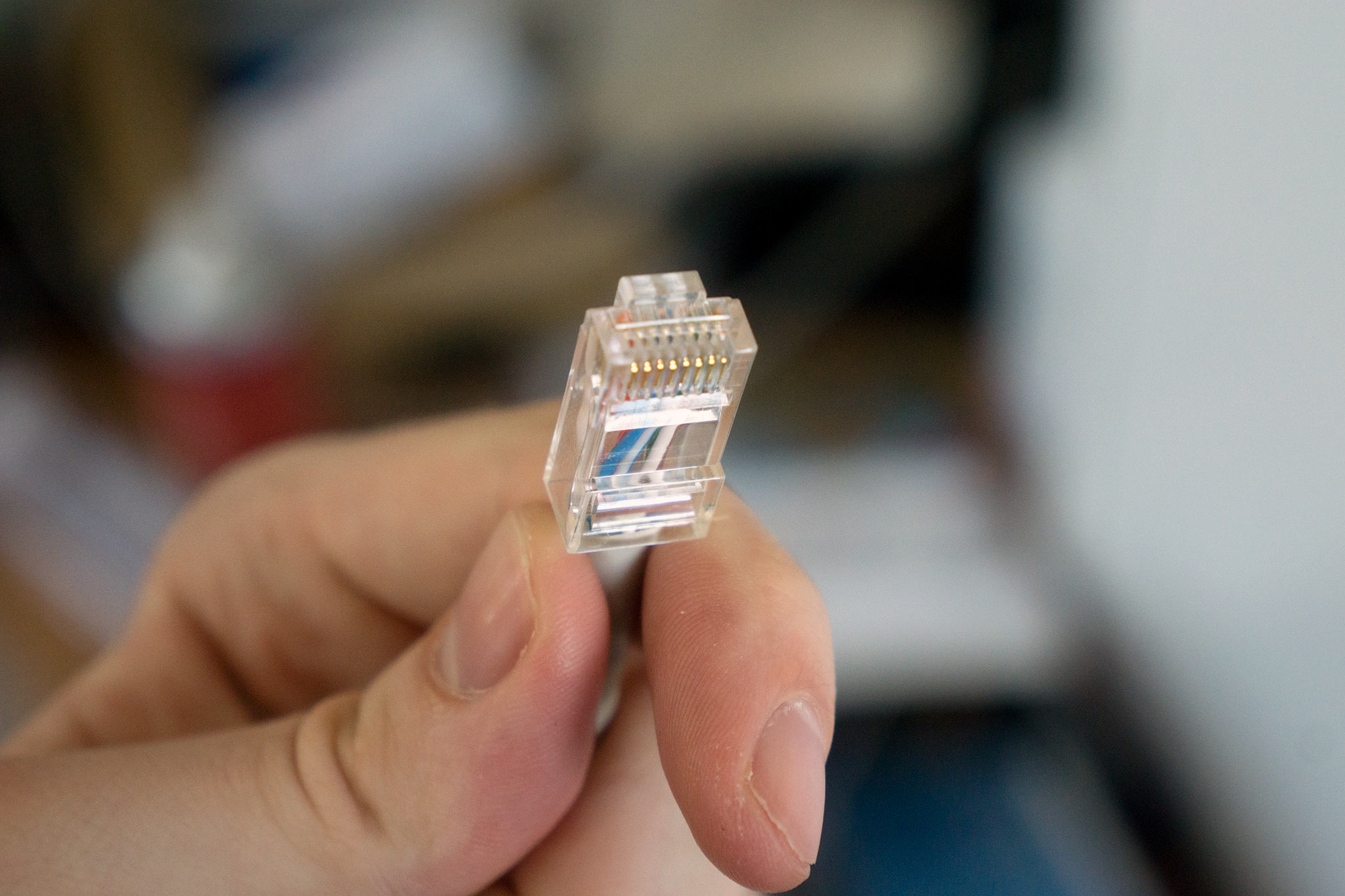
Whether you want to make some cabling of a specific length or just wish to have a little more fun than picking up Ethernet cables from your local store, it's actually an easy and straightforward task to make your own. This process can also help you repair damaged cable in the home or at the office without having to fork out cash for replacements. To get started, here's what you'll need:
- Ethernet cable.
- Crimping tool.
- RJ45 modular connector.
- Cable tester.
For the cabling itself, you can pick up pre-assembled cabling that are ready to use and then cut to size or you could save some more money and pop to your local DIY store who should be able to cut some from a reel for you. You can pick up the crimping tool, modular connectors, and a cable tester in one package:
The cable testing equipment isn't required (you can easily check by connecting the cable to your PC and router), but it makes things easier because you can just reach for a nearby tool and not have to fetch a device.
- Cut the cable to the length you require.
- Using the crimping tool, strip away the cable jacket.
- Check to see if you nipped away at the wires inside.
- Spread the twisted wires out.(The thin thread that joins the four twisted wires allows you to pull the jacket back further, but note that there may be a plastic spine in the middle that requires cutting, along with the wires.)
- Straighten out the wires.
- Line them up in order, using the guides below:Looking at the underside of a connector, the copper contacts are in eight individual slots, numbered one through eight. We're using the T568B standard, which differs slightly from the T568A standard for wiring Ethernet cables.
- Slide the wires carefully into the RJ45 connector.
- Insert the cable into the crimper tool and press hard to secure the connector.
The clamp within the connector should press against the cable jacket. You should not be able to test the cable using the tool or plug each end into a device and see if a connection is made.
Fear not if you don't get the wires lined up perfectly because it can take some practice to get the hang of preventing the wires from overlapping or locking as pairs into the connector. If you make a mistake, simply cut a bit behind from where you were working, and try again.
All the latest news, reviews, and guides for Windows and Xbox diehards.
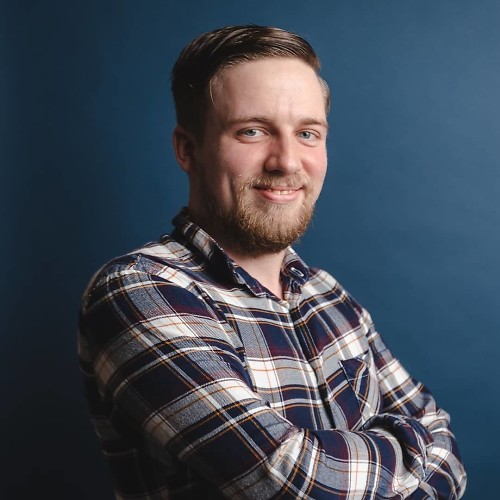
Rich Edmonds was formerly a Senior Editor of PC hardware at Windows Central, covering everything related to PC components and NAS. He's been involved in technology for more than a decade and knows a thing or two about the magic inside a PC chassis. You can follow him on Twitter at @RichEdmonds.